Last Updated on September 8, 2024 by andrewshih
Ever found yourself repeatedly facing the same issue in your projects, despite implementing various solutions?
If so, understanding the Root Cause Analysis 5 Whys technique might be the key to uncovering and addressing the underlying problems effectively.
This method, rooted in simplicity and effectiveness, is a powerful tool for project managers aiming to identify the fundamental causes of recurring issues.
What is Root Cause Analysis 5 Whys?
Root Cause Analysis 5 Whys is a problem-solving tool used to identify the root cause of a defect or problem by repeatedly asking the question “Why?”
The technique was developed by Sakichi Toyoda and is a critical component of Lean manufacturing and Six Sigma methodologies. By asking “Why?” five times (or as many times as necessary), the technique helps peel away the layers of symptoms to reveal the core issue.
The Purpose of Root Cause Analysis 5 Whys
The primary purpose of the 5 Whys technique is to drill down into the core issue causing a problem.
By peeling away the symptoms, project managers can uncover the fundamental cause and implement solutions that prevent recurrence, ensuring long-term success and efficiency.
This method is not just about fixing the immediate problem but about understanding the deeper issues to prevent future occurrences.
When to Use Root Cause Analysis 5 Whys
This method is particularly useful when:
- A problem is recurring, indicating that previous solutions have only addressed symptoms rather than the root cause.
- A quick resolution is required, as the 5 Whys technique is straightforward and does not require extensive data or complex analysis.
- The root cause is not immediately apparent, necessitating a deeper dive into the underlying issues.
- You need to demonstrate problem-solving rigor to stakeholders, showcasing a methodical approach to issue resolution.
Root Cause Analysis 5 Whys in Project Management
In project management, the 5 Whys technique helps in:
- Identifying Project Delays: Understanding the real reasons behind schedule slippages.
- Uncovering Budget Overruns: Determining why projects exceed their financial limits.
- Analyzing Project Risks and Issues: Identifying the root causes of risks to mitigate them effectively.
- Enhancing Process Improvements and Team Performance: Continuously improving processes by addressing root causes of inefficiencies.
Advantages and Disadvantages
Advantages
-
Simplicity: Easy to understand and implement, requiring no specialized training.
-
Effectiveness: Helps identify the root cause quickly, leading to more effective problem-solving.
-
Engagement: Encourages team collaboration and brainstorming, fostering a culture of continuous improvement.
Disadvantages
-
Subjectivity: The outcome can vary depending on who is asking the questions, leading to potential biases.
-
Scope Limitation: May not be effective for complex problems requiring in-depth analysis.
-
Surface Level Analysis: Risk of stopping too early without reaching the actual root cause, especially if the analysis is not thorough.
Steps to Conduct Root Cause Analysis 5 Whys
- Identify the Problem: Clearly define the problem you are facing. A well-defined problem statement helps focus the analysis.
- Ask “Why?”: Question why the problem occurs and write down the answer. This step initiates the process of digging deeper.
- Repeat: Continue asking “Why?” for each subsequent answer until you reach the root cause. Typically, this involves asking “Why?” five times, but it may require more or fewer iterations.
- Document: Keep a record of each step to ensure clarity and accountability. Documentation helps track the thought process and can be useful for future reference.
- Implement Solutions: Develop and implement actions to address the root cause. Ensure that the solutions are sustainable and address the core issue.
Best Practices
-
Be Consistent: Ensure the same person or team conducts the analysis to maintain consistency. This helps in maintaining a uniform approach and reduces variability.
-
Stay Focused: Concentrate on the problem at hand without deviating. Avoid getting sidetracked by unrelated issues.
-
Involve the Right People: Engage team members who are familiar with the issue. Their insights can be invaluable in identifying the root cause.
-
Verify Results: Ensure the identified root cause truly addresses the problem. Double-check the findings to confirm their validity.
Common Mistakes to Avoid
-
Stopping Too Soon: Ensure you have reached the root cause and not just a symptom. Premature conclusions can lead to ineffective solutions.
-
Being Vague: Be specific in your questioning and answering. Vague responses can obscure the real issue.
-
Ignoring Team Input: Failing to involve the team can lead to missed insights and solutions. Collaboration is key to effective problem-solving.
Root Cause Analysis 5 Whys Examples
Example 1: Delayed Project Delivery
- Why was the project delayed?
- Because the team missed a key deadline.
- Why did the team miss the deadline?
- Because the task took longer than expected.
- Why did the task take longer?
- Because the requirements were not clearly defined.
- Why were the requirements unclear?
- Because stakeholders did not provide detailed input.
- Why didn’t stakeholders provide input?
- Because there was no formal requirement gathering process.
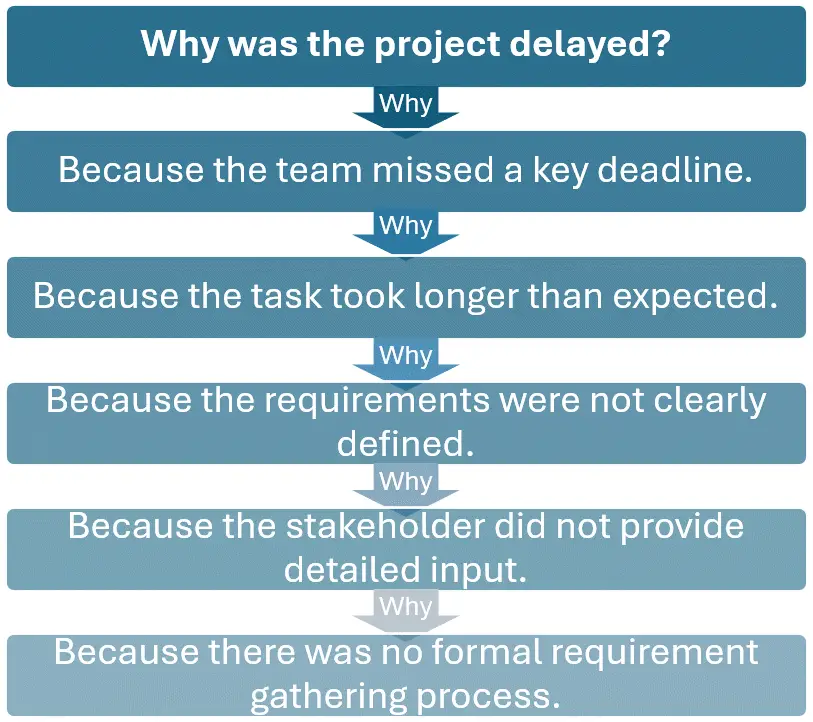
Example 2: Budget Overrun
- Why did the project exceed the budget?
- Because additional resources were needed.
- Why were additional resources needed?
- Because of unexpected scope changes.
- Why were there scope changes?
- Because initial scope was not well-defined.
- Why was the initial scope unclear?
- Because of insufficient stakeholder engagement.
- Why was stakeholder engagement insufficient?
- Because of lack of a structured communication plan.
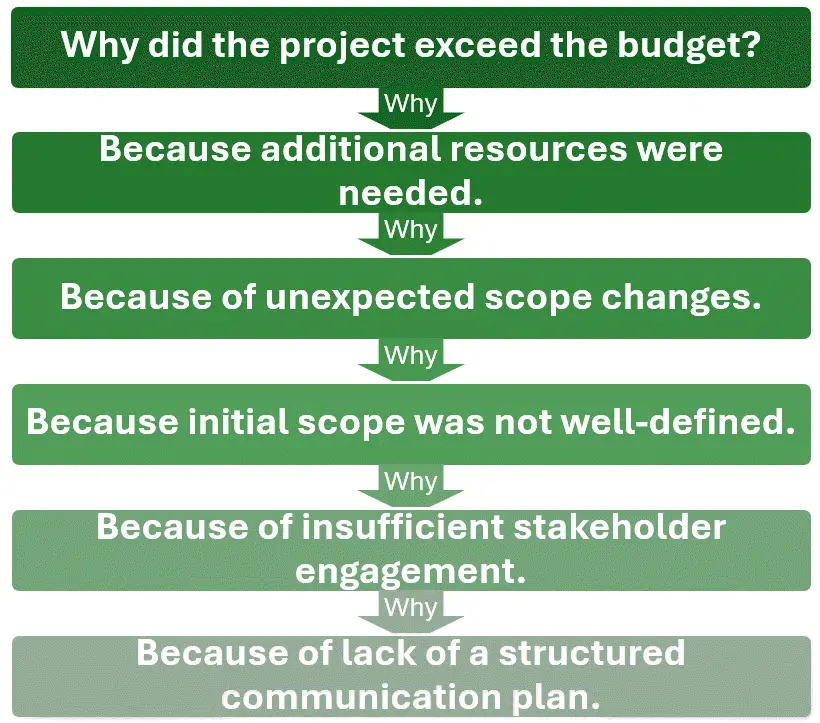
Root Cause Analysis 5 Whys vs Other Techniques Comparison
Technique | 5 Whys | Fishbone Diagram | Fault Tree Analysis |
---|---|---|---|
Complexity | Simple | Moderate | Complex |
Scope | Narrow | Broad | Broad |
Use Case | Identifying single root causes | Identifying multiple causes | Systematic risk analysis |
Visualization | No | Yes | Yes |
Alternatives to Root Cause Analysis 5 Whys
- Fishbone (Ishikawa) Diagram: Useful for visualizing many potential causes of a problem. It categorizes potential causes of problems to identify root causes.
- Fault Tree Analysis (FTA): A top-down approach to analyze system failures. It helps in identifying the various combinations of hardware and software failures that can cause a system failure.
- Pareto Analysis: Focuses on identifying the most significant causes using the 80/20 rule. It helps prioritize the causes of problems to address the most critical ones first.
Tools for Root Cause Analysis
- Root Cause Analysis Software: Tools like RCA Navigator, Root Cause Solver, etc., can facilitate the analysis process.
- Flowcharts: Visual aids to track the sequence of events leading to the problem.
- Mind Mapping Tools: Helps in brainstorming and organizing thoughts, making it easier to identify connections and root causes.
Conclusion
Root Cause Analysis 5 Whys is a straightforward yet powerful tool for project managers.
By asking the right questions and drilling down to the root cause, you can address issues more effectively and prevent them from recurring. Implementing this technique, along with best practices and avoiding common pitfalls, can significantly enhance your problem-solving capabilities and project outcomes.
This method is an essential part of a project manager’s toolkit, helping to ensure that problems are resolved at their source, leading to more successful and efficient project delivery.
FAQ
How many times should you ask “Why?” in the 5 Whys technique?
While the method is named “5 Whys,” you may need to ask “Why?” more or fewer than five times to reach the root cause. The number isn’t fixed but should continue until the fundamental cause is identified.
What if the problem has multiple root causes?
If the problem has multiple root causes, it’s important to address each one separately using the 5 Whys method. Documenting each cause and its contributing factors can help develop comprehensive solutions.
Is there a specific format for documenting the 5 Whys analysis?
There is no strict format, but it’s recommended to use a table or chart to document each “Why” question and its corresponding answer. This helps in visualizing the problem-solving process and ensures clarity.
How can you ensure the accuracy of the 5 Whys analysis?
To ensure accuracy, involve a diverse team with different perspectives, validate each answer with data if possible, and avoid assumptions. Cross-verifying with other problem-solving methods can also enhance accuracy.
What should you do if the root cause identified seems too broad?
If the root cause identified is too broad, break it down further by applying the 5 Whys technique again to drill down into more specific issues. This helps in developing targeted and effective solutions.
How often should the 5 Whys technique be applied in a project?
The 5 Whys technique should be applied whenever a significant problem or recurring issue arises. Regular use can help in maintaining process improvements and preventing future problems.